|
Method 1 Weight ratio The sketch
shown originates from Leonardo da Vinci (ca 1500). He studied
friction by measuring the load hanging on a cord, at which the block
begins to slide. The coefficient of friction is found by the
quotient of the
dead weight of the mass hanging on the cord and the mass of the block, i.e.
µ = Ff / N = mdead weight / mblock
|
Static coefficient of friction - dynamic coefficient of friction The moment at which the block begins to slide
(break away force) is the so called static
friction, the force at which the block continues to
slide is the dynamic or kinetic
coefficient of friction. For most material combinations the value of
the static
friction exceeds that of the dynamic friction. Be aware that the
dynamic friction can still be dependent on velocity, contact
pressure, temperature and surface roughness. The static friction can
be dependent on the time that the block is in rest, which is
typically the case when lubricated. |
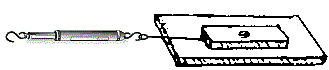
Method 2:
Spring balance
Pull a spring balance connected to the block and slowly increase the
force until the block begins to slide. Make sure the spring balance
is parallel to the surface.
The reading on the spring balance scale when the load
begins to slide is a measure for the static friction, while the
reading when the block continues to slide is a measure of dynamic
friction. The
coefficient of friction is simply µ = Fspring /Fnormal
= Fspring /(mblock ·g
), g=9.81 m/s²
|
Hint: Pulse rotation sensors (multi-turn potentiometers,
pulse encoders) often prove to be very
useful to create low cost sensors for
measuring displacement by
combining the sensor with a cable and a pulley, for
measuring torque
with a torsional spring, for measuring force with a wire, a pulley
and a spring etc. |
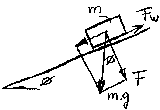
Method 3: Tilted plane
Place a block on a tilted plane and increase the angle of tilt until the block begins to slide. The tangent of the tilting angle
just found is the so called "friction angle". This angle is related
to the coefficient of friction µ, i.e. µ = tanų = Ff /F
|
Method 4: Clamping To measure the static coefficient of
friction under conditions of high contact pressure the object may be
clamped between two surfaces. The force necessary to put the
object in motion must be halved to obtain the friction force because
of the two contacting surfaces.
|
Method 5: Pendulum
The
pendulum is suitable to analyze the static and dynamic friction
under reciprocal motion by monitoring the bearing torque. This
however requires a torque sensor. The energy loss of combined static
and dynamic friction can be analyzed by considering the reduction of
the amplitude of motion in time. This only requires a simple rotary
potentiometer or pulse rotation sensors to visualize the amplitude
reduction in time.
|
Method 6: Motorized Tribometers
In the measuring methods discussed above the friction coefficient
is measured in fresh contacts, not after running in. The
coefficient of friction may change significantly during first
half hour of sliding. The time necessary to obtain a stable value
of the coefficient of friction can be observed in a motorized tribometer by monitoring the friction over time. This method
is
common for measuring the specific wear rate and the contact temperature
during operation. You may visit the useful links on the right of
this window to find more information about motorized tribometers. |